Guide to buying a used hill-sider combine
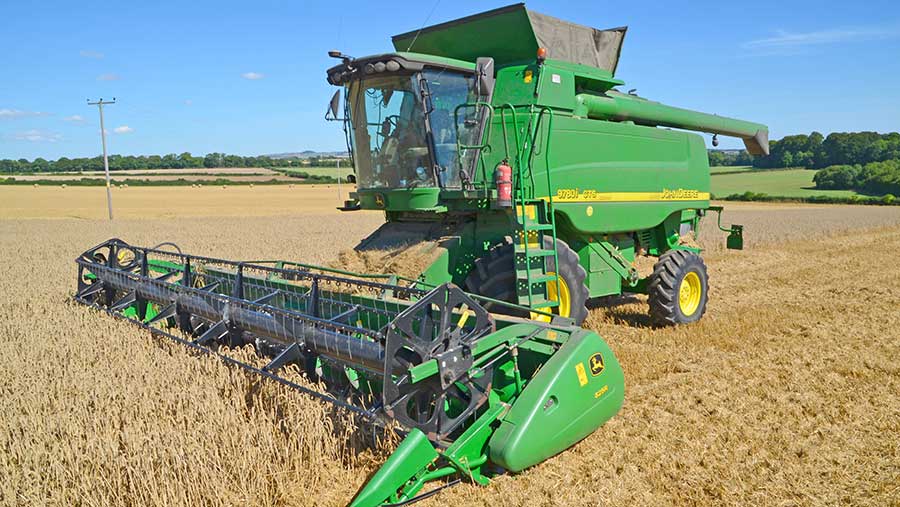
True full body levelling on combines is not just a nice-to-have feature – for some farms it’s essential.
And although the additional cost when buying new isn’t as much as you’d expect, used machines can carry a pretty high premium.
That said, there are bargains to be had if you do your research. We’ve talked to dealers across the more undulating parts of the country that sell a big proportion of their combines equipped with side-slope compensation, both new and second-hand.
See also: Driver’s view: Nick Brown’s John Deere S790i combine
What’s available?
If you’re looking at proper body levelling then your choices are a little limited.
Until recently, Claas had restricted its Montana system solely to its Lexion models, although it now offers it on its mid-range Tucanos, too.
Similarly, for years New Holland had chassis correction on only its smaller TC-type machines and stuck with sieve levelling for the more mainstream models.
However, in the past couple of years it has offered Everest body-levelling system on certain CX and CR models.
In contrast, AutoLevel has been an option on most Massey models for the past 30 years or so. Similarly Deere has offered Hillmaster slope compensation on virtually all of its combines since the early 1990s.
Meanwhile, Deutz and Laverda have quietly worked away in the background with their own hill-sider models.
Cost
When you talk to dealers of all colour preferences, there’s one common theme between them. A true body-levelling system isn’t as expensive an option as you might imagine.
Generally, slope compensation will add £10,000-£15,000 to the on-farm price which, although not to be sniffed at, isn’t a huge proportion of the final bill when you’re shelling out several hundreds of thousands on a machine.
The critical thing here is what that does for residual values. When you talk to those in the second-hand trade you can generally expect to pay a similar premium for a combine equipped with body-levelling, so anyone buying new won’t see that money evaporate in depreciation.
Of course there are the obvious benefits of having a hill-sider – reduced losses, increased output on slopes and improved traction. But on top of that, speccing a combine with body-levelling often brings extras that you would otherwise have to pay more for.
For example, on a Claas combine the Montana system includes diff-lock and header pitch control, enabling the operator to tilt the table fore and aft – a real bonus when trying to scoop up laid crops.
And it might seem blindingly obvious but hill-siders have to have header lateral tilt as a matter of course, and often that’s included in the package price, too.
So there are multiple benefits in having a tilting body combine but what are the pitfalls for someone looking at one second-hand? Surely, after 10 or 15 years work, all the extra moving parts and complexity create their own headaches?
We talk to the experts to get an idea of what to look out for. (For the purpose of this article we’ve focused on Deere, Massey and Claas machines as those three brands would account for the lion’s share of combines sold with true body-levelling).
More extreme options
More extreme hill-siders capable of clambering up the side of mountains are offered by most manufacturers.
These tend to be smaller machines, but in the US you’ll find specialist firms converting big rotaries to run on side slopes of up to 27deg. Search Hillco Technologies online.
John Deere Hillmaster
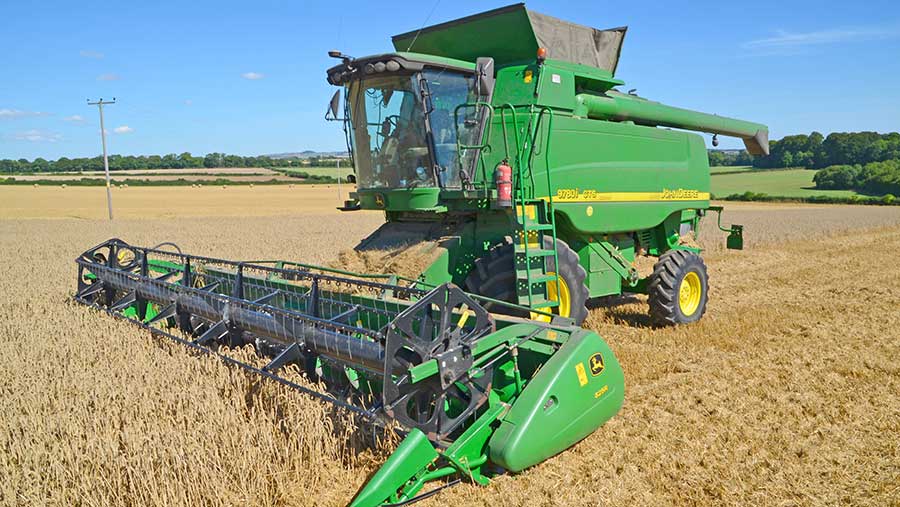
© Nick Fone
The basic principles of Deere’s Hillmaster system have remained fairly well unchanged for decades and share much in common with the other set-ups on the market.
The final drives can rotate around the front axle, effectively acting as eccentric cams, with rams independently raising the left and right hand sides of the machine.
An inclinometer measures slope angle and sends oil to the appropriate lift cylinder to level the combine out.
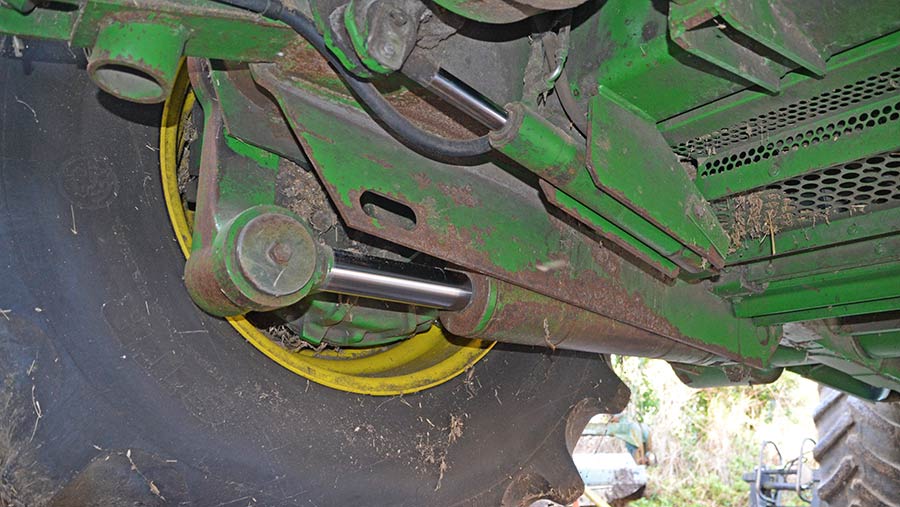
A compensator ram linking the swivelling right-hand final-drive to the chassis displaces oil in a closed circuit to the header lateral tilt ram, aiding the cutterbar contouring system to respond to changes in body angle © Nick Fone
Compensator ram
A compensator ram linking the swivelling right-hand final-drive to the chassis displaces oil in a closed circuit to the header lateral tilt ram, aiding the cutterbar contouring system to respond to changes in body angle.
The whole arrangement only employs a total of five grease nipples – one on each final drive mounting, one on each lift cylinder and one on the compensating ram.
Among the few daily lube-points, these can get overlooked with the result that the bushes can run dry.
Simply raising and lowering each side of the machine via the in-cab computer will identify this – it will tend to judder as the rams extend and retract.
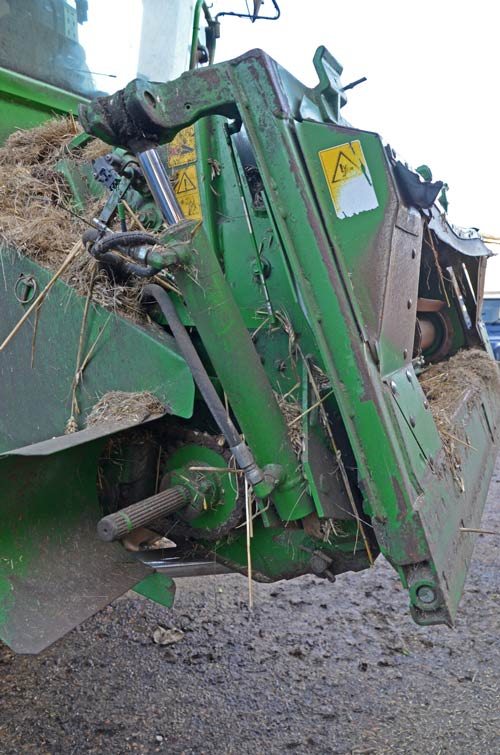
On the feeder housing the pivoting face-plate is very similar to that on a flat-land combine equipped with lateral tilt, the only difference being a longer-stroke cylinder that provides a greater degree of left-to-right travel © Nick Fone
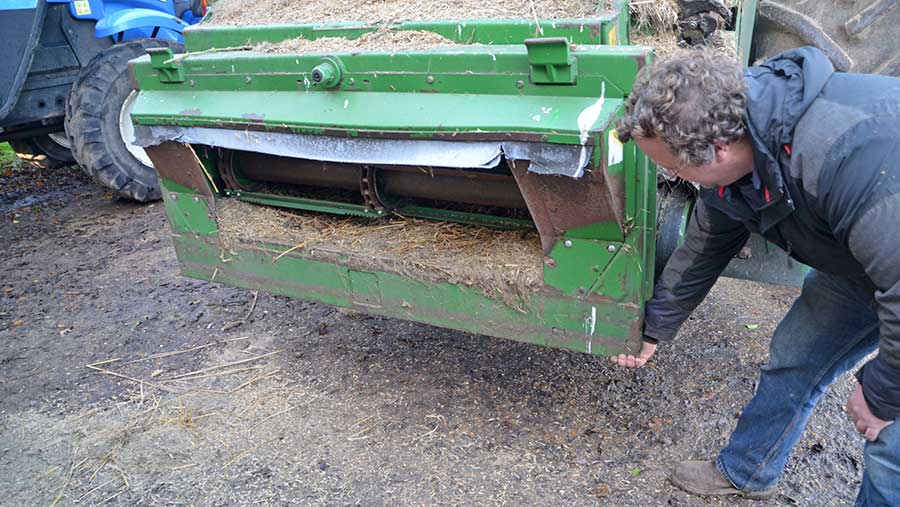
Knock out one of the lateral tilt ram’s pins and check that the pendulum swings freely… © Nick Fone
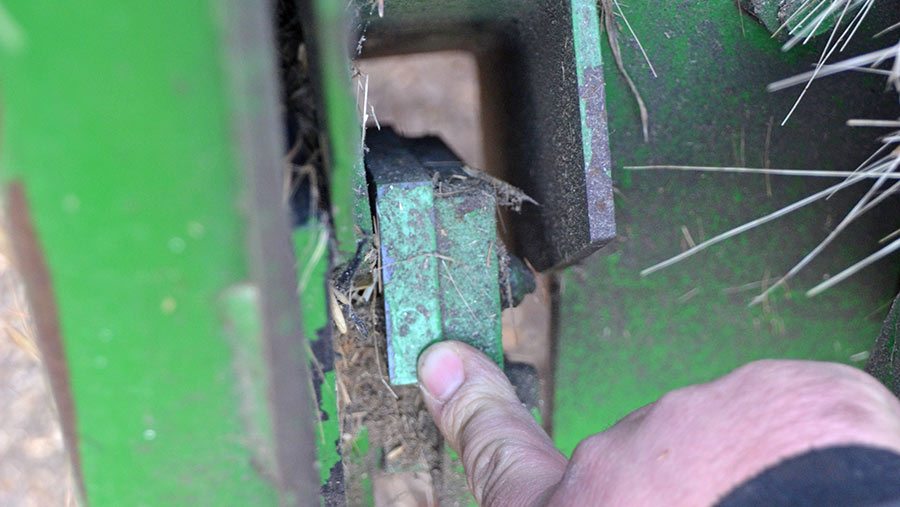
..if it doesn’t move easily by hand (right) it suggests the wear-pads in behind the plate have been damaged as a result of pulling backwards with the header on the ground to clear blockages or recover a bogged-down machine © Nick Fone
Pivoting face-plate
On the feeder housing, the pivoting face-plate is very similar to that on a flat-land combine equipped with lateral tilt, the only difference being a longer-stroke cylinder that provides a greater degree of left-to-right travel.
Wear plates in the bottom of the face-plate can be damaged if the machine has experienced trauma, often as a result of getting bogged down.
If the header has been dragged backwards while in contact with the deck then the wear-plates will suffer. Knock out a pin at one end of the lateral tilt ram and then try to pivot the face-plate by hand. It should swing freely from its upper pendulum pivot point.
Similarly, check the mounting points for the compensating ram alongside the right-hand wheel – if they are bent or twisted or there is evidence of welding on the castings, it indicates it has received excessive pressure at some point, most likely as a result of trauma.
Controls
On Hillmasters built between 2003 and 2012 the system is controlled by a simple box positioned under the returns elevator, independent of all the other combine electronics.
Containing a gyroscope slope monitor and a very straightforward bang-bang valve, it sends oil in the appropriate direction to level the combine.
Calibration couldn’t be much simpler – manually set the combine to level using a spirit level and then slacken off the bolts securing the box, set it level and tighten it back up.
Later models
Post-2012 things got a bit more complex, with the levelling system integrated into the main corner-post computer. The control valve then became proportional, enabling much finer adjustment of the body.
Within the system is the ability to set the ‘dead-band’ – the point before which the valve will start to level the machine.
The way to check it’s all working as it should is to manually override it and then allow the combine to return to its upright position.
Because of the way the system works, it will initially make one large movement and then two subsequent corrections to fine-tune it. Don’t be perturbed if you get two or three adjustments – that means the system is working as it should.
What to pay?
There’s no hard and fast guide as to what to pay for Hillmasters but, as an example, at the time of going to press there was a 2010 W660 HM with 6.2m (20ft) header advertised online with 1,470 engine hours and 1,040 drum hours for £75,000.
Google also flagged up a 2012 T560 HM with 6.6m (22ft) header, Starfire GPS, rape extensions, 1,550 engine hours and 1,100 on the drum for £88,000.
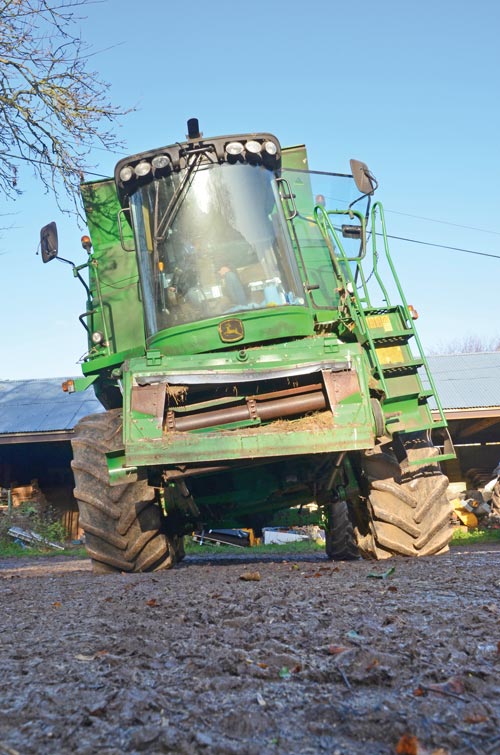
With all colours of hill-siders jack them up left-to-right and feel for any juddering that might indicate the bushes might not have received a regular dose of grease © Nick Fone
Massey Ferguson Autolevel
Massey Ferguson’s Autolevel slope compensation system has been available on all of the brand’s models since the early 1990s.
While it was pretty revolutionary for its time, little changed over the subsequent two decades and, in truth, it wasn’t able to cope that well with the increased demands from larger, high capacity combines.
Like the Deere system, pivoting final drives provide the levelling function, but the header lateral tilt compensation is achieved in a slightly different way.
The rams used are double-acting-type cylinders but, rather than providing positive lift force, the top side of the piston displaces oil to the opposing cylinder, helping to level the body.
To do this it runs through a complex aluminium valve block that also diverts oil off to the single lateral tilt ram.
While this arrangement worked well when it was first introduced on the combines of the early ‘90s, as harvester and header sizes grew its weaknesses became apparent.
A good number of machines would tend to creep in one direction so that the operator would constantly have to tweak the levelling system manually.
Thankfully, Massey provided a spirit level in the cab for this purpose. But it wasn’t an easy task, requiring the driver to navigate their way through the Datavision computer’s various menus to find the appropriate page while going along.
When turning on the headlands it could also struggle to react fast enough to counter the change in slope direction with the result that the machine would often be coming back into work tilted over in the wrong direction.
This would result in the header making contact with the ground, forcing oil back through the system and sometimes shearing the piston from its rod or splitting the aluminium valve block.
These were issues common to many of the larger models, much to the frustration of many Massey dealers. Controlled via the in-cab computer, little could be done to improve the situation other than altering the response rates, often to little effect.
Many operators became resigned to the situation, waiting patiently on the headlands for the system to get its ducks in a row before setting off on the next run.
Disappointingly little changed when Massey switched production from the Dronnenborg plant in Denmark to the Italian Laverda factory in 2010, re-badging the Cerea range as the Centora.
However, smaller Laverda-derived Activa and Beta Autolevel machines didn’t tend to suffer this issue to the same extent.
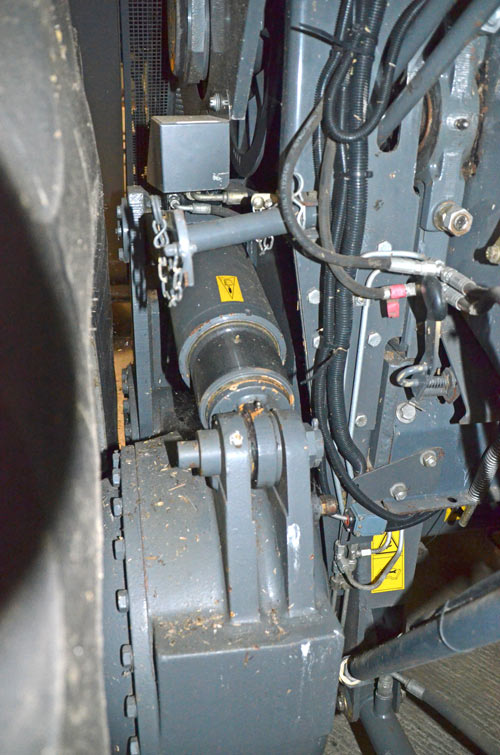
On Laverda-derived Massey AutoLevel combines the body levelling rams are positioned over the axle, up out of the way of debris and damage
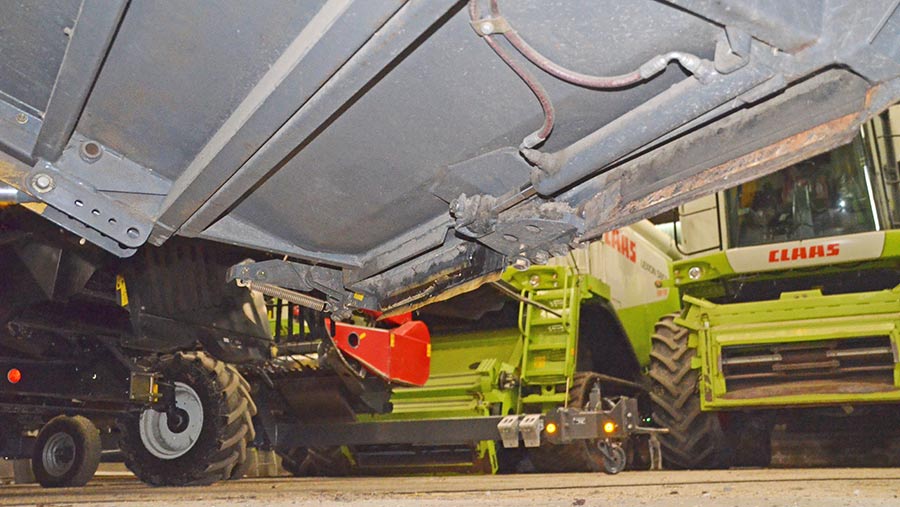
A single tilt-ram under the intake elevator face-plate provides lateral tilt for the header and is plumbed into the AutoLevel hydraulic circuits to compensate for body movements
System revamp
The whole system was revamped 10 years ago. Most significantly the company ditched the traditional rotating final-drive arrangement to level the body off and switched to wishbone-style hub mountings with driveshafts sandwiched between two triangular parallelogram linkages.
Dubbed ‘Paralevel’, the key advantage of this approach was said to be that the wheels would rise and fall perpendicular with the ground rather than in an arc, reducing side-loadings on the wheels, hubs and axles and maintaining a constant surface contact with the ground.
At the time, MF also hinted that it could enable the fitting of tracks – a first for any hill-side machine.
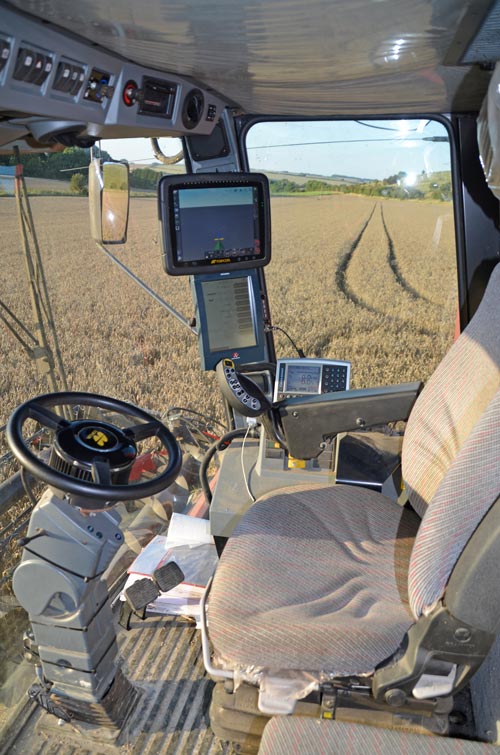
Massey Ferguson Cerea cab
What to pay?
Aside from the issues with Autolevel, second-hand Massey hill-siders offer good value for money second-hand. A quick web trawl will turn up results pretty promptly.
For example, at the time of going to press there was an eight-walker 2012 Centora 7282 AL advertised with a 7.5m (25ft) PowerFlow header, 1,700 drum hours and 2,100 engine hours for £53,000.
Similarly a smaller five-walker 2008 Activa 7245 AL with 5.4m (18ft) cut and just 900 drum hours was on offer for £64,000.
Claas Montana
Dubbed Montana, Claas’s body-levelling system has been available on selected straw-walker and hybrid Lexion models for a couple of decades.
Much like other manufacturers’ approaches, it uses rotating final-drives to raise and lower each side of the combine independently.
This arrangement generally proves pretty robust and trouble-free, although it does require greasing. Jack the machine up and rock it backwards and forwards to detect any excessive play in the hub mounting bushes.
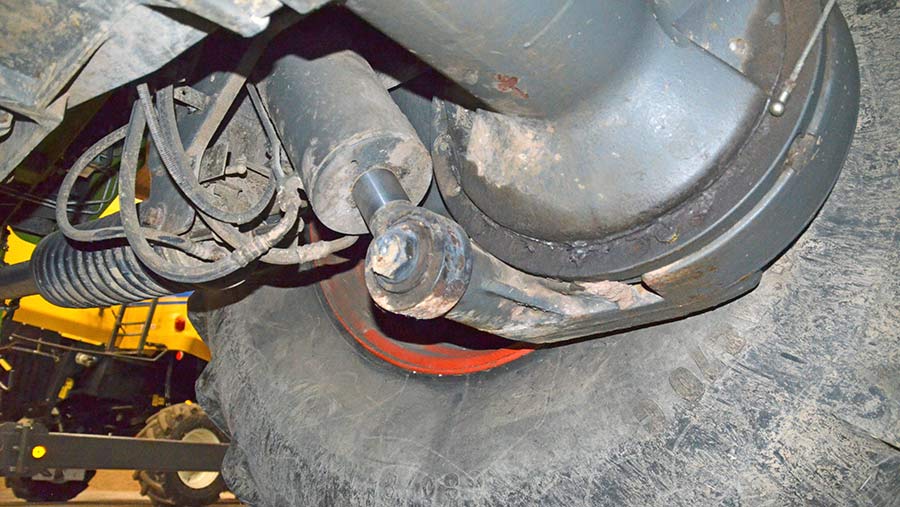
Beefy rams rotate the Lexion’s final-drive to raise and lower each side of the combine. You can see this one has been well greased
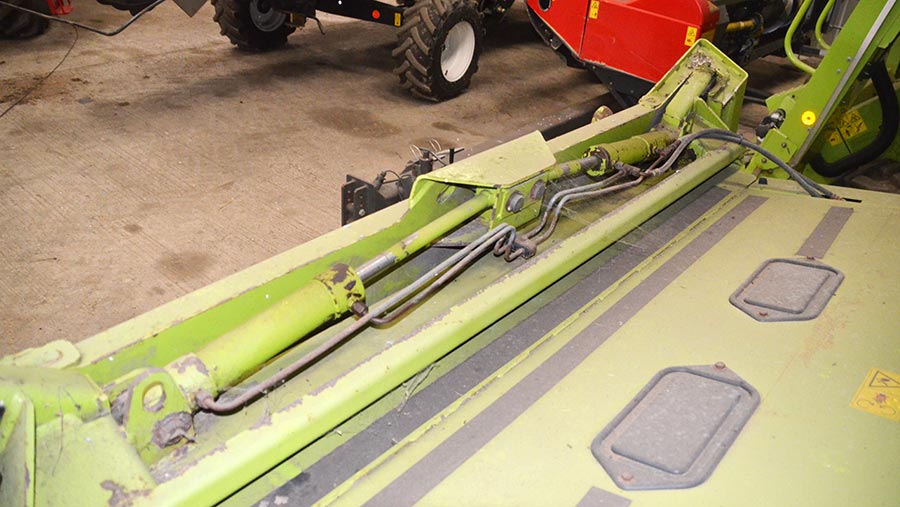
Up until the launch of 600 and 700-series Lexions, Montana models had extra lateral tilt rams across the top of the feeder housing to provide additional header tilt
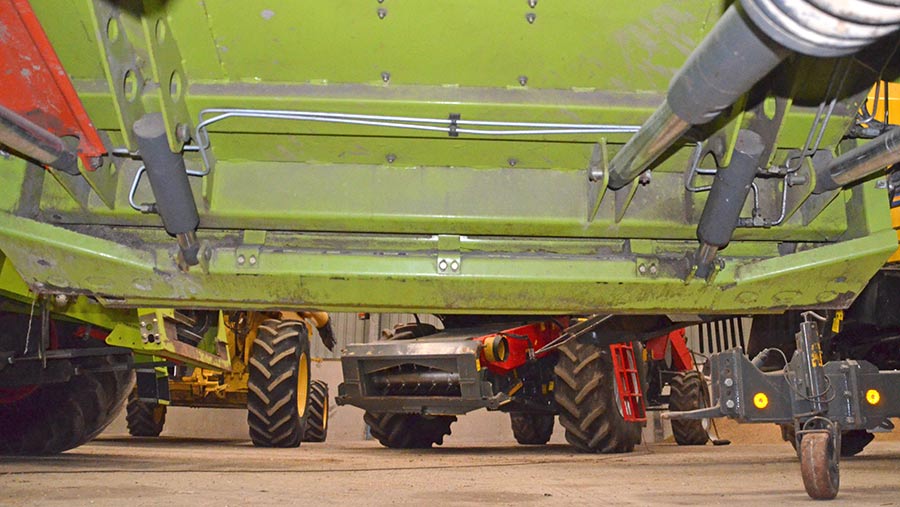
Montana spec brought with it a number of extras, including header tilt -0 a useful feature to aid in scooping up laid crops
Elevator face-plate
Where the Claas system differs from the others is with the intake elevator face-plate.
While standard machines had a pair of stubby rams at either side to provide lateral header tilt, these were joined by an extra brace of cylinders mounted horizontally on the top of the trunking to provide extra travel to compensate for the increased combine body movement.
Check around the outside of the header mounting frame for cracks or welds as this is an area that receives a fair bit of stress. Thankfully it’s easy to access and rectify any weaknesses with a dose of electric glue.
Header pitch control
In addition to this, Montana spec also included header pitch control. With a pair of rams under the header attachment carriage, the fore/aft angle of the cutterbar can be tweaked to compensate for longitudinal body movements.
It’s also a very handy addition when trying to pick up laid crops, especially if you want to avoid fitting lifters.
The system is controlled by an extra electronic module and valve-block that gets a feed from inclinometers on the axle mounting frame and sends oil to the appropriate rams to level the body. At the same time it keeps the header faithfully hovering over the stubble.
The only regular issue that tends to rear its head is physical damage to the axle height sensor linkages. Relatively delicate, these exposed devices couple the rotating final-drives to potentiometers on the chassis.
If the combine gets bogged down or straw builds up under the body these can get knocked and bent so that they don’t provide a true reading and the system won’t level the combine precisely.
A simple calibration in the Cebis computer can sort this, otherwise it’s new sensors and linkages.
Up to the end of 500-series Lexion production, Montanas had a different transmission to standard models. Rather than the conventional three-cog box, hill-siders got a two-speed unit with a two-stage splitter.
This provided an extra ratio for hill-climbing, although operators still had to come to a standstill before shifting gear. Montana customers also got the benefit of a diff-lock – a real bonus for hill-climbing.
What to pay?
Given that this hill-sider set-up only tends to add £10,000-£15,000 to a new machine, the extras that come with Montana really start to stack up. Expect to pay at least a £10,000 premium for a second-hand Lexion with body-levelling.
That plays out when you start keying the words ‘Montana combine’ in to any search engines. We turned up a 2006 550 M with 1,500 drum hours and a 6.7m (22ft) Vario header advertised at £80,000.
At the other end of the spectrum, sneaking in just under our £100,000 limit we found a Lexion 750 M with 1,340 engine hours, 830 drum hours and 9m (30ft) Vario header listed at £94,000.
Acknowledgements
Thanks to Devon-based used combine specialists Steve and Rodney Cowle, Lincs-based Kevin Kirby, Smart Ag Services’ Andy Miller and Morris Corfield’s Darren Duppa.