How a pig farmer is using bag tanks to improve slurry storage
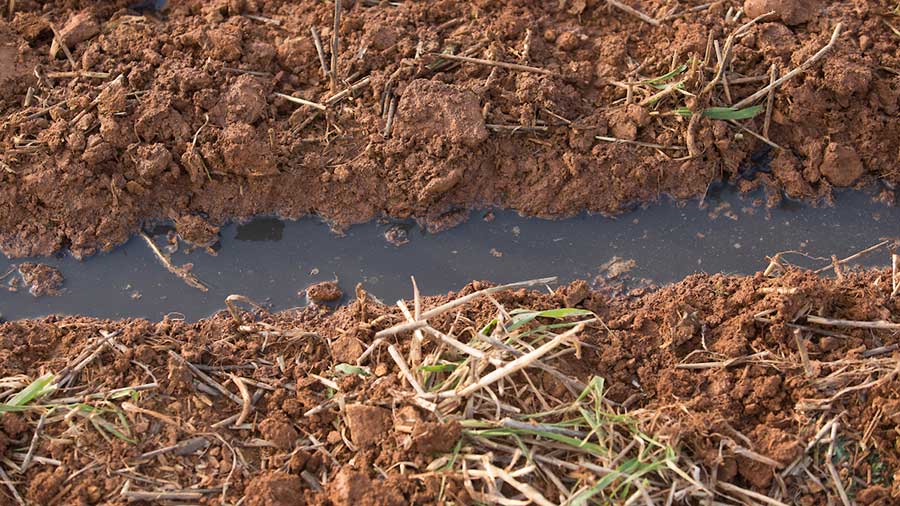
A system of bag tank storage is putting a large-scale pig producer a step ahead of legislation that will require slurry stores to be covered by 2027.
Pig farmer Andrew Corrigan has three bags ranging in volume from 2,000cu m to 7,000cu m for storing slurry from the 3,600 sows at two breeding sites in the north of England.
The units operate with an environmental permit and must adhere to strict limits on emissions. To achieve this, the business opted for slurry bags which offered a lower-cost alternative to a covered lagoon.
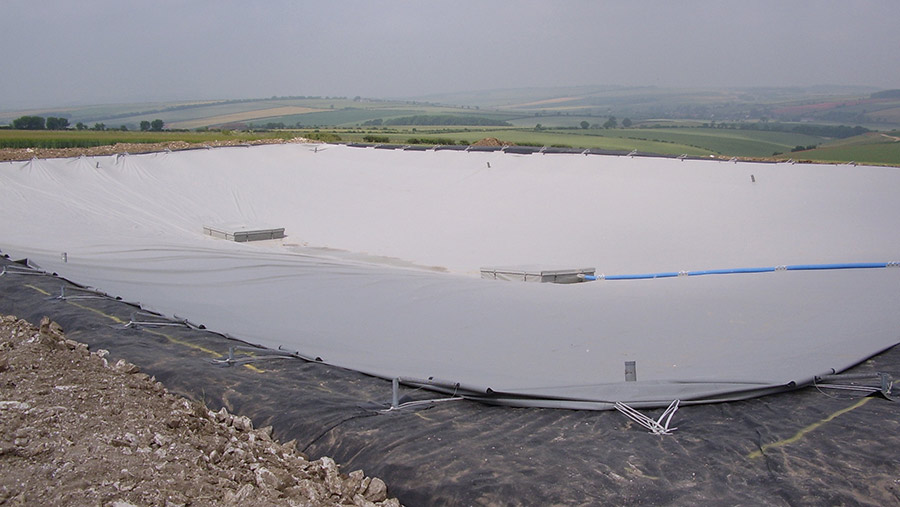
© Albus Alligators
From 2027, it won’t only be farms with environmental permits that will have to comply with restrictions on emissions – all slurry and digestate stores in England will need to be covered.
See also:Â Advice on planning your slurry storage requirements
Farm facts
- 870 hectares (2,149 acres) farmed
- 3,600 breeding sows
- Farrow-to-finish system
- Arable rotation of winter wheat, winter barley, spring barley, oilseed rape, rye, peas and potatoes
- 80,000 laying hens
There are obvious cost implications from this legislation, but Mr Corrigan advises farmers to balance this downside with the slurry nutrient value to be gained from preventing ammonia being released.
“We rely on the nitrogen in the slurry to grow our crops – we want it on our land not in the air,” he explains.
Switching from straw to slats
One bag was installed eight years ago and a further two in the past three years, when the business expanded.
Each slurry bag takes about four to five days to install, once the groundwork has been completed.
The system switched from straw-based finishing to slatted sheds with automatic ventilation. But straw is still used for outdoor-bred sows to maximise the value of straw from the arable rotation.
The investment in the slatted system has paid off – on average, there is a 0.3kg feed conversion rate gap between the two systems because the controlled climate is better for growth.
“Our best straw site is on a par with our worst slatted unit,” says Mr Corrigan.
Slurry storage
The conversion, which included an expansion in sow numbers, required an increase in slurry storage.
The farm was pleased with the performance of its Albers Alligator tank, so it opted for two more from Tramspread.
“We priced up a covered lagoon and, for us, it was going to cost approximately double the price of a slurry bag – although that won’t necessarily be the case on all farms, it depends on the site,” says Mr Corrigan.
With each bag purchased, he has scaled up in size. The 7000cu m tank is on the smallest site, but it is an expanding unit. The 3,500cu m bag was about ÂŁ100,000, and the 7000cu m was in the region of ÂŁ140,000.
“We have learned from experience that whenever you need storage for slurry or muck, you might as well double the requirement at that time.
“Scaling-up [storage] gives us flexibility. If we have a year of terrible weather, we are not limited to six months storage – we probably have enough for a year,” he adds.
Siting the bags
The bags are made of strong polyester fabric coated on both sides with a plastic, waterproof layer, and fitted with fill and empty pipes and mixers.
There are two options for siting the bag – a shallow pit is needed, so either a hole must be dug or an embankment built around a flat piece of land.
Mr Corrigan says the key is to ensure that the site work is done well and that the soil is suitable.
“You need a good digger operator and the right soil – a solid sandy clay.
“One of our sites was on very chalky ground, so we needed to import a lot of sand to line the bed or the bag would have torn or worn against stone over time.
“But we also have one on clay land which was almost fit for purpose. We didn’t need sand and there was an embankment there.”
Installation and benefits
The bags were delivered on a flatbed trailer, with the 7000cu m model weighing about 8t, and a team of 14 people rolled them out.
“You pin the bag down like you would peg a tent, and you then start pumping slurry into it,” Mr Corrigan explains.
As it fills, it rises above the hole it sits in. When it is 1m above ground, it has reached capacity. Capacity takes longer to achieve than in an open lagoon because there is no rainwater entering.
The surface area of the biggest bag is 30x60m. “That is quite a lot of area for the rain to fall on if it was open to the elements,’’ Mr Corrigan points out.
The absence of rainfall is a definite upside, he adds.
“Slurry has a nutrient value, but if it was mostly water there would be little benefit to soils.”
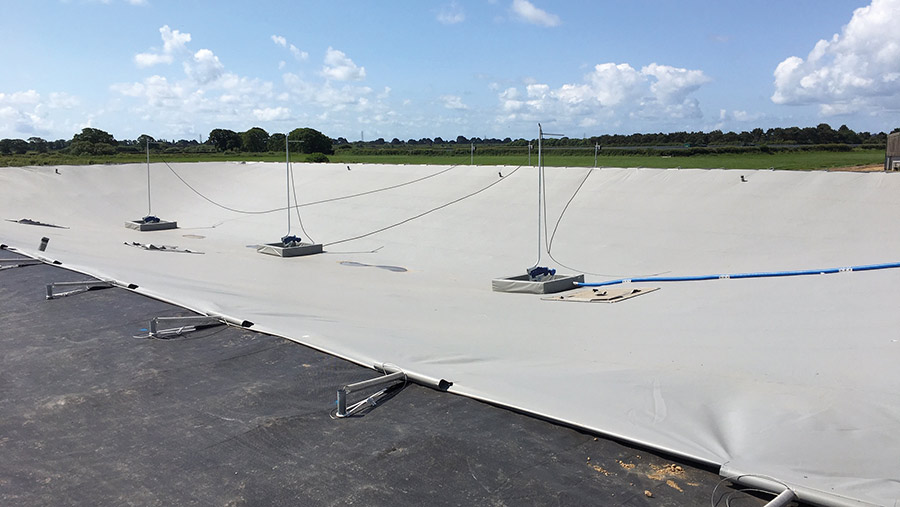
© Albus Alligators
Management considerations
The slurry must be managed better than in a lagoon. If it isn’t regularly stirred, solid material will build up and a digger can’t get inside the bag to alleviate this.
This is despite the fact the pig slurry is quite liquid because of a high level of washing down between four-week batches of pigs, says Mr Corrigan.
Slurry is stirred all year round to prevent solids from settling.
The farm has installed three-phase stirrers, which are bolted onto the concrete base at the centre of the pit to ensure frequent stirring as the bags fill up. There are three stirrers in the biggest pit.
Once the slurry gets to a certain level, the stirrers are activated by a timer which operates during the night to utilise cheaper electricity.
The tanks can be supplied with hydraulic stirrers but, because the farm has three-phase electricity, Mr Corrigan says this was the best option.
“In the early days, we did use hydraulic stirrers, but these were putting a lot of hours on the tractor. Even if a farm doesn’t have three-phase electricity, I think they would be better off getting a generator than running the stirrer off a tractor.’’
Before drawing the slurry ready for spreading, it is stirred continually for one week.
Slurry bag tanks – the pros and cons
Pros
- Lower cost than a covered lagoon
- Often doesn’t require planning permission, but advisable to check if consent is needed
- The slurry is fully contained and always covered
Cons
- Slurry needs to be well-managed to prevent the build-up of solids
- Takes up more land surface area proportionately to volume than a raised tank
- Lifespan can be shorter than a permanent concrete tank, if the bag is not looked after