Solar-powered robot drills and weeds on Shropshire farm
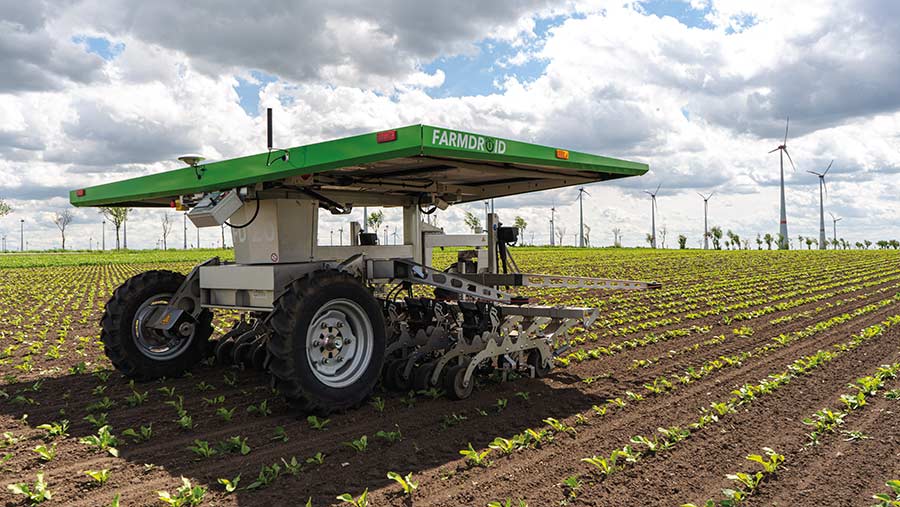
The launch of a new farming robot now seems a near-monthly occurrence, with universities, manufacturers and inventors across the globe on a mission to replace people with autonomous machines.
The problem with virtually all these cutting-edge, high-tech projects is that they’re just at the concept or testing stages – a good five or 10 years off commercial reality. But there are a few exceptions, and it’s no coincidence that two of them hail from the same shores.
The first is Agrointelli’s Robotti, which has been developed by a team from the east coast of Denmark.
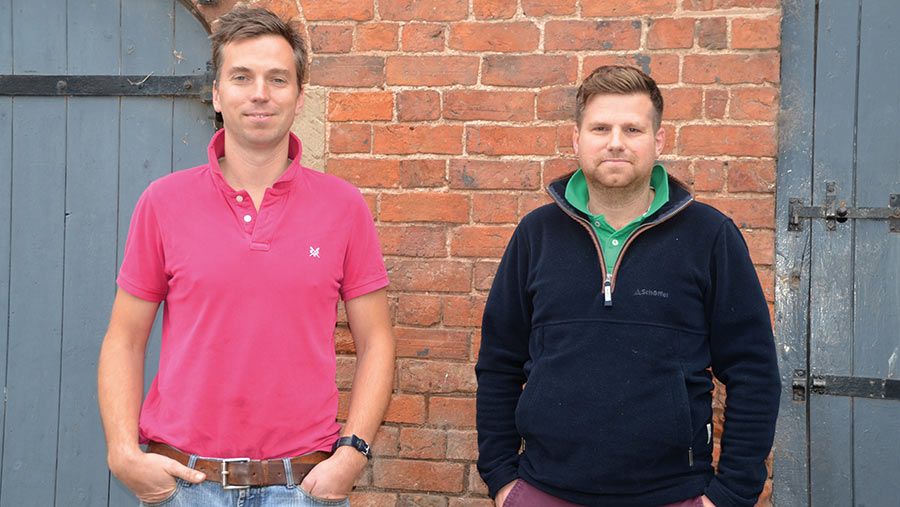
Chris and Ed Brettell © Nick Fone
A completely unmanned unit, it uses diesel engines to provide the muscle and can carry conventional implements on its three-point linkage. Earlier this year, Suffolk vegetable producer Home Farm Nacton took delivery of the first Robotti to hit the UK.
Danish farming brothers Jens and Kristian Warming have taken a slightly different approach in the development of their Farmdroid concept – a dedicated seed ’n’ weed robot capable of precision sowing and then hoeing on subsequent passes.
It is solar-powered and completely self-sufficient, using RTK-corrected GPS signals to record where each seed is planted, rather than complicated weed-identification camera technology
On the following weeding runs it knows what is a crop plant and what isn’t, purely by its location and without using any cameras or sensors. Its electronically activated blades then work the soil, both between and within the rows.
Farm facts
FS Brettell and Son, near Shrewsbury, Shropshire
- Farmed area 445ha, all organic
- Cropping 182ha spring oats, 60ha winter oats, 40ha fodder beet, remainder in grass leys
- Livestock 12,000 laying hens
- Machinery Tractors – MF 8S225, MF 7720, MF 7616; loader – Merlo TF 42.7; combine – Claas Lexion 760; drill – 6m home-built power-harrow combi with FarmForce front tank; weeders – Garford inter-row hoes with camera guidance (one for beet, one for cereals), Farmdroid FD20 six-row beet drill/hoe
- Staff Shane, Chris and Ed Brettell plus two more full time
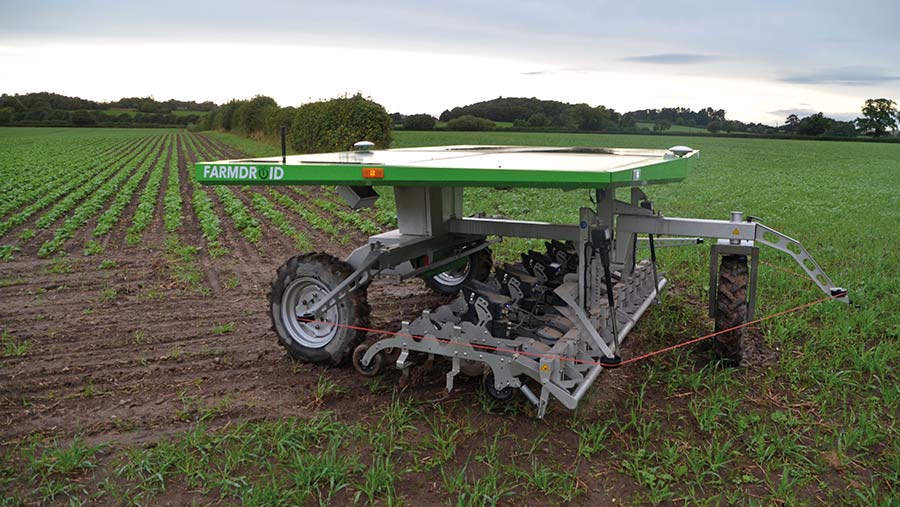
© Nick Fone
The simplicity of this approach has helped get it to market relatively quickly compared with the highly complex robotic weed-seeking systems currently being developed by the big players. To date, there are more than 160 Farmdroids out working across Denmark, Germany and now the UK.
At the beginning of June, the first one arrived in Shropshire at the Brettell family’s organic arable enterprise.
“While power-harrowing this spring, I had plenty of time to think about ways we could improve our approach to beet establishment and weed control,” explains Chris Brettell.
“After a bit of internet trawling, I stumbled across a video of the Farmdroid working. I immediately knew it was what we needed. I loved the fact that being solar-powered means it is completely energy self-sufficient and that the simple approach of recording where seeds are planted allows it to accurately weed between the crop plants in the row.”
Two months later, a lorry pulled up in the yard carrying the UK’s first Farmdroid. Mid-lockdown, it was up to the Brettells to get the unit up and running on their own. But with guidance provided over the phone from Denmark, it turned out to be a surprisingly straightforward task.
Initially, it is carried to the target field and around the boundary on its three-point linkage, enabling it to register the field shape and allowing the operator to input any obstacles. This is all displayed visually via a smartphone app, where it is possible to tweak the position of the geofence. Then it’s just a case of filling the drill hoppers with seed and pressing the “go” button.
“It was strange to see it set off on its own for the first time, doing six rounds of the headlands before turning in to the long work.
“It was quite remarkable that within a few hours of being here it was up and running. Calibration was dead easy, and at a basic level that’s one of its biggest plus-points – the seeding units are super simple.
“Rather than using a vacuum, a shutter opens and shuts at timed intervals, which results in really accurate spacing. It’s the best singulation I’ve seen from any precision drill.”
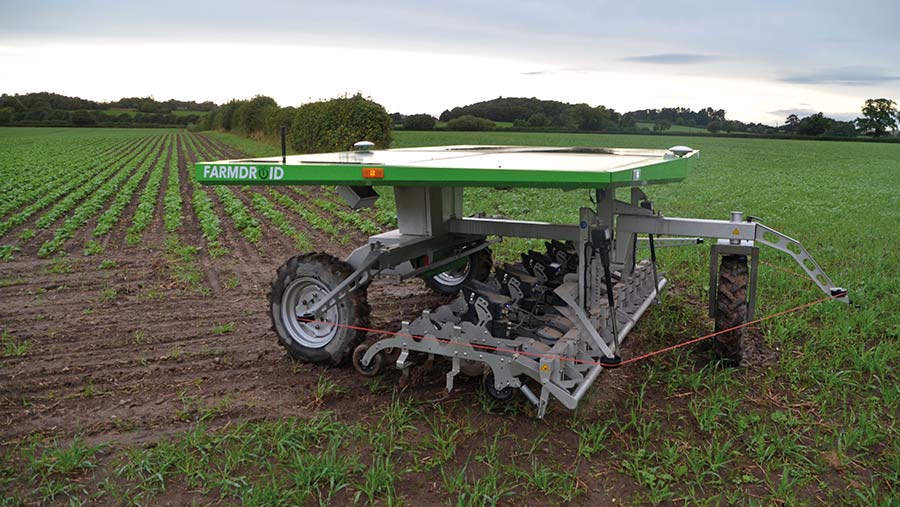
© Nick Fone
How does it work?
With its own RTK base station, the GPS-guided machine can record exactly where it places each seed. Because it works at such a slow speed it is able to achieve sub-1cm accuracy levels.
That is critical in enabling it to do a decent job on subsequent weeding passes. Between each crop row, arrow-shaped tines slice through any weed growth like a cheese-wire – it’s basically just an ultra-shallow inter-row hoe.
The clever bits are the solenoid-actuated in-row weeder blades. These shunt in and out between the recorded position of each crop plant, eliminating any weeds growing where they shouldn’t be.
One of the big advantages of using the approach of recording plant positions rather than weed-seeker camera technology is that the Farmdroid can go straight to work weeding the moment it has finished drilling.
It doesn’t need to be able to “see” the crop rows or the weed seedlings. By starting the weed-control process at such an early stage, it ensures they don’t have the chance to establish a root structure.
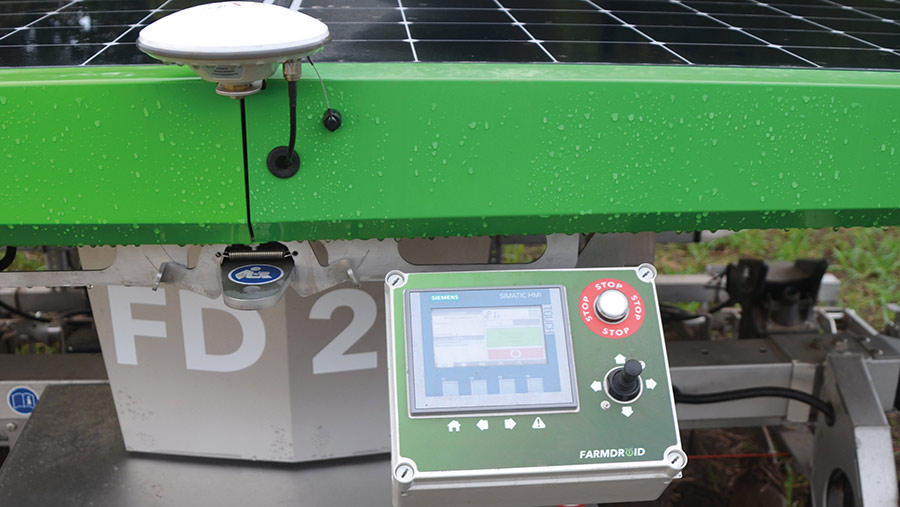
© Nick Fone
What speed does it run at?
In drilling mode, the six-row Farmdroid will generally travel at 500m/hr. It then ups the pace to between 650-800m/hr when it’s weeding.
That equates to 0.15-0.2ha/hr, which might not sound that impressive, but over a 22-hour working day it adds up to 3-4.5ha.
How long is the battery run-time?
Because the Farmdroid’s solar panels recharge the batteries as it trundles along, it can work pretty much indefinitely – as long as there’s sunlight.
The company says most units working predominantly in spring cropping will average 20 hours/day. The closer it gets to 21 June, the longer the working day, and it may only need a single hour off in the middle of the night.
What crops can it drill and weed?
It was originally developed by the Warming brothers to sow and weed sugar beet, but growers of alternative crops have been quick to see its potential, and have put units to work in onions, herbs and salads.
This high-value, labour-intensive produce is seen to offer the greatest opportunity, but the Danish firm is working on versions for more mainstream crops.
A 12-row machine with 22.5cm row spacings has been developed for cereals, although it is limited solely to inter-row weeding rather than in-row work. There is also a large-seed version with wider row spacings in the pipeline that should be able to handle maize, beans and even peanuts.
This season, Farmdroid has also been working with one big-name player to test a bolt-on sprayer that could be used to make spot applications of herbicides, fungicides and insecticides. Initial reports suggest such a setup could have the potential to reduce agrochemical use by up to 90%.
How do the figures stack up?
With a headline price of €65,000 (£55,540) plus another €10,000 (£8,540) for the RTK base station, the capital cost of the Farmdroid isn’t huge when compared with the investment in a tractor, precision drill and camera-guided inter-row hoe such as the Garford Robocrop.
The Brettells know this only too well, having previously had to run through their crops of organic fodder beet repeatedly to try to keep on top of weed growth.
“Even with the Garford’s half-moon discs working in the crop rows we would struggle to really keep the fat hen under control, so not only did we have the expense of multiple hoe passes, but often we’d have to hand-rogue at a cost of £100/acre,” says Ed Brettell.
“The Farmdroid does away with these issues, as it is capable of working to within 5mm of each beet seedling between the rows and 20mm in the row.
“Not only are we saving on roguing and weeding, but there has been a definite increase in yield. By the end of the season, we can see a huge difference in the root size – where, previously, we’d be getting 50-60t/ha, it’s now more like 80-100t.”
What are the downsides?
“Honestly, it’s difficult to think of many negatives,” says Chris.
“Obviously, without anyone at the helm it’s very dependent on GPS, and if that drops out it will come to a standstill. So, when you’re initially setting out the fields, you need to give trees a really wide berth to avoid ‘satellite shadows’.
“The other potential shortcoming is the slow work-rate when drilling. If you’re up against it because the weather is closing in, the 0.2ha/hr pace could cause frustration and, unfortunately, you can’t just go out there with a tractor-mounted drill to push on, because the robot then won’t know where each seed is placed for its weeding passes.”
The verdict?
“Given that the Farmdroid arrived mid-lockdown and we had no one here on site to help with setup, we were impressed with how intuitive it was to do and the backup we got over the phone from Denmark,” says Chris.
“Since then, it’s worked faultlessly. If it needs a software update, it’ll do it itself and carry on with the job.
“Admittedly, it was late in the season when it arrived, so we only had 2.5ha of beet left to sow, but that provided the ideal test site. We’ve since put it to work drilling and weeding a further 2.5ha of stubble turnips, which it has done without a glitch.
“Next year, we’re going to try to push it to do our entire fodder beet area. That’s double the 20ha Farmdroid recommends, but we’re confident it will manage it based on this year’s performance.”
- Reports from organic sugar beet growers in Germany suggest each Farmdroid can comfortably handle a 30ha workload, and 40ha at a push. Some have units covering 60ha, but have seen a detrimental effect on yields with the robots unable to keep on top of weed pressures.